In high vacuum (HV), ultra-high vacuum (UHV), and extreme high vacuum (XHV) applications, the importance of surface finishes extends far beyond aesthetics. While visually appealing surfaces are often prized in various industries, when it comes to vacuum applications, the functionality of a surface finish can significantly impact the performance, reliability, and longevity of equipment. This blog delves into the critical aspects of functional surface finishes tailored for vacuum environments, highlighting their application and purpose.
Table of Contents
The Role of Surface Finishes in Vacuum Applications
- Outgassing Reduction: One of the primary concerns in vacuum systems is outgassing, the release of gasses trapped within materials. Surface finishes play a crucial role in minimizing outgassing by providing a barrier that inhibits gas release. Polished and coated surfaces are particularly effective in reducing outgassing rates.
- Surface Cleanliness: Cleanliness is paramount in vacuum applications. Contaminants on surfaces can outgas or migrate within the system, compromising vacuum levels. Specialized cleaning protocols and surface treatments such as sonic baths are employed to achieve ultra-clean surfaces that maintain vacuum integrity.
- Mechanical Properties: Surface finishes can enhance the mechanical properties of materials, such as hardness, and wear resistance. This is particularly important in vacuum environments where components may undergo significant thermal and mechanical stresses.
- Improved Surface Sealing: A smooth surface finish can increase the seal life by reducing wear on a seal and improving overall performance. Additionally, surface finishes can impart changes to material hardness impacting the wear of the seal on the sealing surface.
- Thermal Management: In high-vacuum conditions, thermal conductivity becomes a critical factor. Surface treatments that improve thermal emissivity or conductivity can aid in managing heat within the system, ensuring stable operation.
- Electrical Conductivity: For applications involving electrical components, surface finishes that enhance electrical conductivity are essential. This ensures reliable performance of sensors, detectors, and other critical electronic components in a vacuum.
Challenges in Developing Functional Surface Finishes
Creating functional surface finishes for vacuum applications involves several challenges:
- Material Compatibility: The surface treatment must be compatible with the base material to ensure adhesion and longevity. This requires precise selection and application techniques. This is particularly true of electropolishing and anodization.
- Environmental Stability: The surface finish must withstand the harsh conditions of the vacuum application environment, including extreme temperatures, radiation, and chemical exposure.
- Precision and Uniformity: Achieving a uniform surface finish is crucial for consistent performance. This demands advanced manufacturing techniques and stringent quality control.
Types of Surface Finishing for Vacuum Applications
In vacuum applications, manufacturers employ several specialized surface finishing techniques to meet the stringent requirements of HV, UHV, and XHV environments. Here, we explore some of the most effective methods:
Machined
Machined refers to a surface finish typically accomplished as a result of the manufacturing process. This finish is the result of production from a mill or lathe, most commonly applied to flanges and other sealing surfaces. In the context of vacuum applications, a machined finish offers several advantages:
- Surface Smoothness: Modern CNC machine can achieve very smooth finishes, reducing the sites where contaminants can adhere or gases can be trapped.
- Material variety: Machined finishes can be applied to a variety of metals making it a versatile solution for a surface finish.
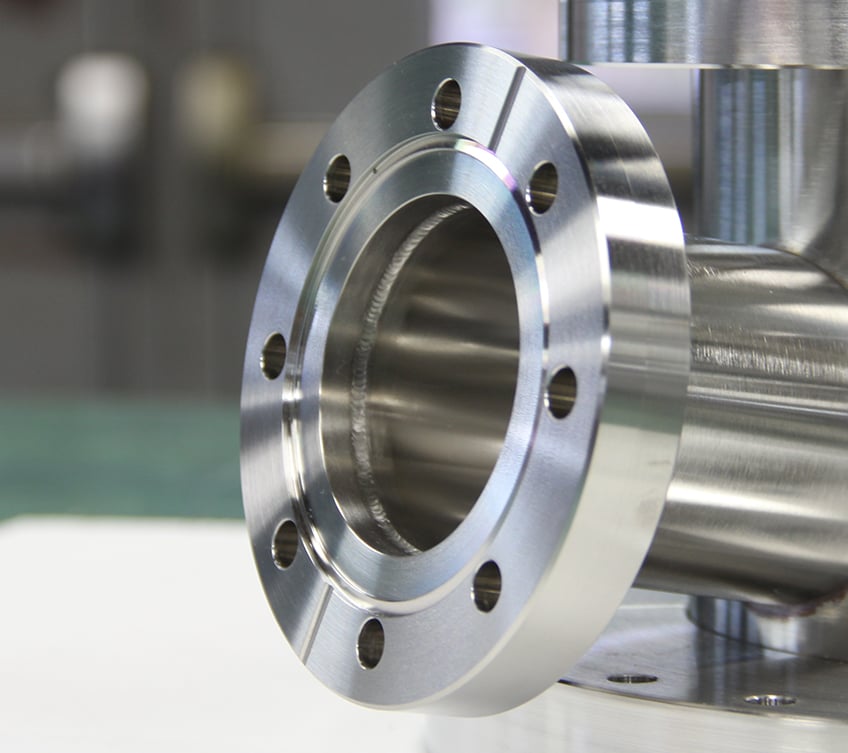
Mechanically Polished
Mechnically polished finishes from ANCORP are available in brushed and random orbital styles. Brushed mechanical finishes result in a shiny, grained finish on the metal as a result of the grit level used. The random orbital style refers to a collection of applications using sanders and produces a swirled grain pattern on metal. Of the two, brushed mechanical finishes tend to feature more shine on the surface. Advantages to mechanically polished vacuum components include:
Brushed Mechanical Polish:
- Directional Surface Texture: The linear finish can help channel any contaminants away from critical areas.
- Aesthetic Appeal: Provides a visually consistent and attractive surface, which can be important for equipment that requires a clean appearance.
Random Orbital Mechanical Polish:
- Uniformity: Produces a consistent finish that is free from noticeable patterns or lines.
- Surface Smoothness: Helps in reducing microscopic peaks and valleys, which can trap contaminants or gases.
Machined or mechanically polished finishes are a pre-requisite surface treatment to Electropolishing.
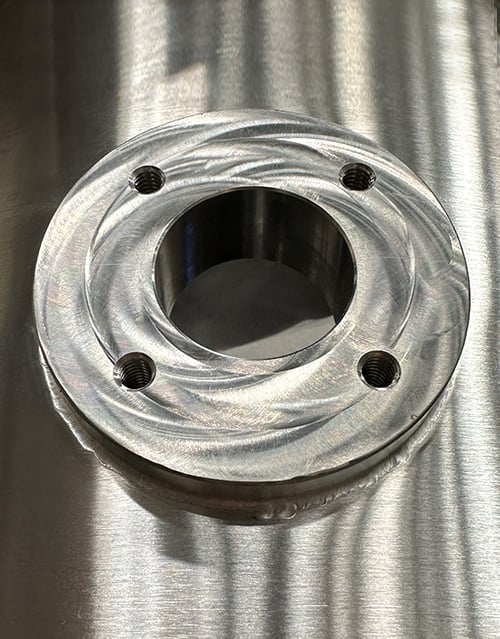
Electropolish
Electropolishing is an electrochemical process that removes a thin layer of material from the surface of a metal, resulting in a smooth and highly reflective finish. This process is particularly beneficial for vacuum applications due to the following reasons:
- Outgassing Reduction: By smoothing the surface at a microscopic level, electropolishing minimizes the number of sites where gases can be trapped, thereby reducing outgassing.
- Surface Cleanliness: The process removes contaminants and oxide layers, resulting in ultra-clean surfaces that are crucial for maintaining vacuum integrity.
- Corrosion Resistance: Electropolishing enhances the corrosion resistance of metals, which is vital for the longevity and reliability of vacuum components.
Determining if electropolish is right for you relies on understanding the intricacies of the application environment and process.
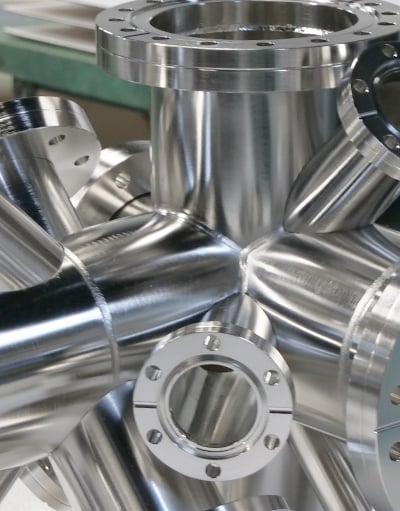
Glass Bead Blasting
Glass bead blasting, also known as abrasive blasting, involves propelling a stream of abrasive material against a surface to clean, roughen, or smooth it. This method is particularly useful in vacuum applications for the following reasons:
- Surface Preparation: Bead blasting effectively removes surface contaminants, oxides, and other impurities without significantly altering the base materials.
- Texture Control: It can create a uniform surface texture, which is beneficial for applications that require specific surface properties.
- Improved Adhesion: By roughening the surface, sandblasting can enhance the adhesion of subsequent coatings, ensuring they bond more effectively and uniformly.
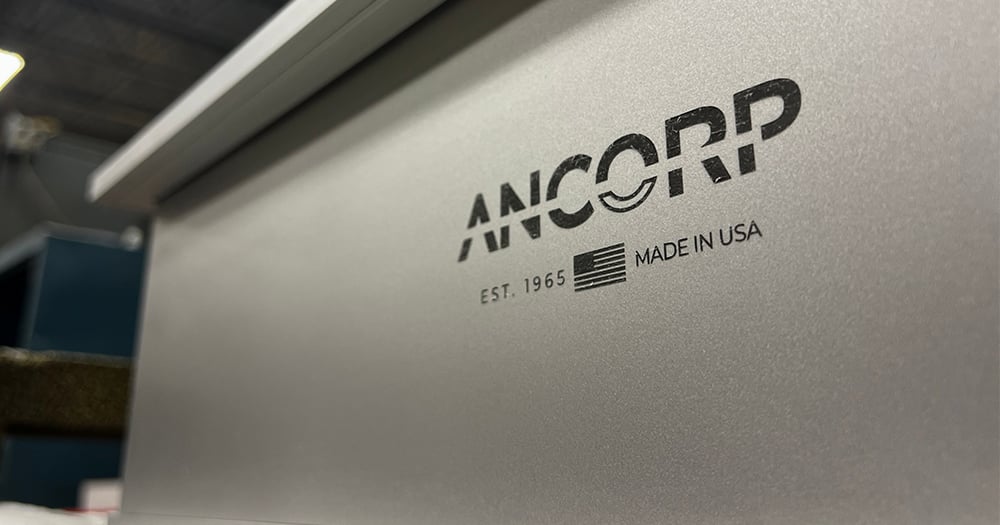
Anodization
Anodization is an electrochemical process that increases the thickness of the natural oxide layer on the surface of metal parts, typically aluminum. This method offers several benefits for vacuum applications:
- Corrosion Resistance: Anodized surfaces are highly resistant to corrosion, which is essential for components exposed to vacuum environments.
- Enhanced Durability: The anodized layer provides a hard, wear-resistant surface that extends the lifespan of components.
- Electrical Insulation: Anodization can create an electrically insulating layer, which can be beneficial for vacuum applications where this is required.
- Customization: Anodized finishes can be done in various colors, providing both functional and aesthetic options for vacuum components.
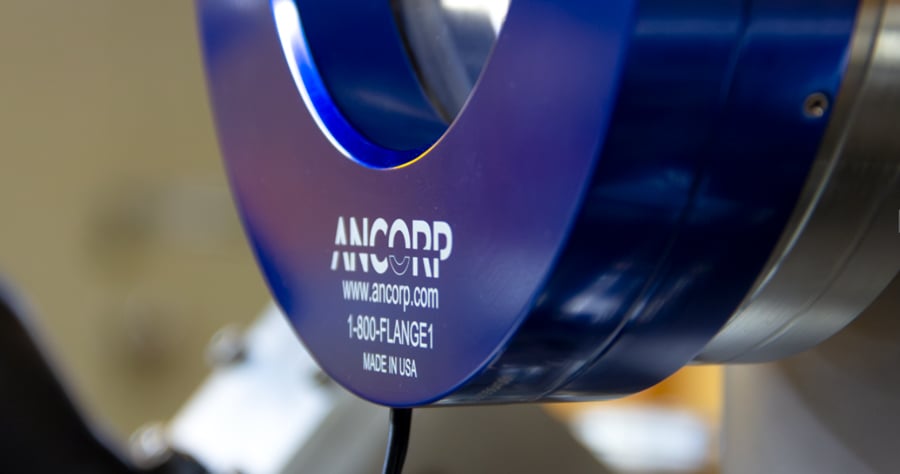
Conclusion
In conclusion, surface finishes in HV, UHV, and XHV applications play a crucial role in ensuring the performance, reliability, and longevity of vacuum systems. Techniques such as machining, mechanical polishing, electropolishing, glass bead blasting, and anodization address specific challenges like outgassing, surface cleanliness, mechanical properties, sealing efficiency, thermal management, and electrical conductivity. By understanding and implementing these specialized surface treatments, engineers and technicians can significantly enhance the functionality of vacuum components, meeting the stringent demands of advanced vacuum environments.
For ordering information on surface finishes, please contact our sales team at sales@ancorp.com or begin a live chat. Our application engineers are here to help you select the right finishing solution for your vacuum application needs.